Keywords: hardness tester heat treatment industry heat treatment heat treatment is to improve and ensure the quality and reliability of mechanical products, improve the competitiveness of the manufacturing industry, one of the important basis, the level of its industry level plays a pivotal role in the development of the manufacturing industry. At present, China's heat treatment industry, in addition to a few manufacturers, the overall level is far from being able to adapt to the more fierce market competition environment that the heat treatment industry faces after joining the WTO. Among these, China's heat treatment testing equipment is even more backward. Severe limitations and hinders the development of process technology and the instability of product quality. What is more important is that it can not effectively prevent unnecessary quality accidents in products. Below I will give an example of the most commonly used hardness test after heat treatment of mechanical parts and tooling.
Hardness is an indicator of the hardness and hardness of metallic materials. The hardness value is not actually a physical quantity of a unit. It is a comprehensive performance of a series of different physical quantity combinations that characterize the elasticity, plasticity, deformation, strengthening rate, strength and toughness of a material. The indicator, generally considered hardness, refers to the ability of the metal surface to resist deformation and cracking in a small volume. The practical value of using the portable Leeb hardness tester for hardness testing is that it is not necessary to destroy the workpiece and batch test the parts. It has become one of the important experimental methods for product quality inspection, establishment of a reasonable process, and analysis of product quality.
I have been working at the heat treatment production site. According to the use conditions and the use of the Leeb hardness tester, I think the Leeb hardness tester is a combination of push and rebound hardness values. It has unique structure. The wide range of practicality, especially the hardness value and failure analysis of large and medium-sized and complex-shaped workpieces and tools, has the advantage that other types of hardness testers cannot be replaced.
Structural parts and molds test the actual use of a, using the Leeb hardness test hardness test to verify, verify large gear shaft, ring gear pretreatment process and carburizing quenching process method:
1, after the pretreatment process test
The quality of this process operation directly affects the uniformity of the hardness distribution of the pinion and the ring gear inner carburized layer after the carburizing process and the deformation of the teeth. More important is the strength of the core (not penetrated). When using the Leeb hardness tester to test the inner diameter and end face of the pinion and shank of the pinion and the outer ring inner diameter of the ring gear, if the hardness difference between the highest and the lowest in the same area of ​​the test is found, the temperature of the instrument is checked and the furnace is installed. Under the premise that the process cooling method is normal, it can be inferred that there is segregation or banded structure in the workpiece within the workpiece according to the difference in hardness value and the distribution status. Strips segregated as shown in the metallographic picture
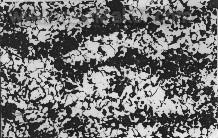
Because the actual test with the hardness method is that the test point is high in the hardness of the black pearlite belt, and the hardness of the white ferrite belt is low. This structural defect is impossible to eliminate in the subsequent carburizing and quenching operation, but is retained. Once this large-scale pinion and internal ring gear have such defects, it will not only result in a short service life when installed, but also cause major equipment accidents. When we can infer the strip segregation in the forging by testing the hardness method, we can use the solution treatment process or other processes to eliminate the strip segregation immediately to eliminate the defects, thereby preventing equipment accidents and reducing losses.
2, after the carburizing process test
The final heat treatment process of this process toothed pinion and ring gear, usually the inspectors only test the HRC hardness of the sample, as shown in the figure:
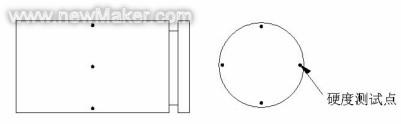
Then the samples were cut for metallographic analysis: permeation layer martensitic grade, carbide grade, morphology distribution, retained austenite amount morphology, core martensite grade, and microhardness tester was used to test the penetration layer from the surface layer. To HV550 hardness above deep depth operation as final inspection. However, from the accident analysis of the early failure of the tooth shaft and the serious wear of the tooth, it was found that the physical hardness was lower than the hardness of the sample, especially when it occurred in deep carburizing. The reason is that the actual pinion, ring gear and The sample is not cut off from the same block, nor is it pretreated by the same furnace. In this way, the original structure of the material and the sample before infiltration are different, and there is a certain difference between the microstructure and hardness after the infiltration. The main reason is that during the entire carburizing process, due to the great differences in the surface area of ​​the workpiece and the carburized area (chemical heat treatment absorption) The interfacial reaction of the process and the main factors include the concentration of each component of the infiltrating medium and the surface state of the workpiece, the surface shape, the surface area size, and the surface energy that have an extremely important influence on the chemical heat treatment process.) Tested hardness on the Leeb hardness tester Compared with the hardness measured by the Rockwell hardness tester and the microhardness tester on the sample, combined with the metallographic analysis of the sample penetration layer, the cause of the quality problem can be found quickly and accurately. Combined with necessary process adjustments, accident hazards can be eliminated before the workpiece is assembled.
Second, use the Leeb hardness tester to test the hardness of large and medium-sized complex structure mold technology
This is a feed mold made of martensitic stainless steel and is mainly used to produce feed. There are 10,000 to 27,000 holes in the mold, and 10 tons of mixed feed powder per hour is extruded from the die hole area into pellets. Therefore, the critical control point for the quality and service life of the ring die is the hardness and penetration of the die area in the ring die. The following are physical pictures of die wear:
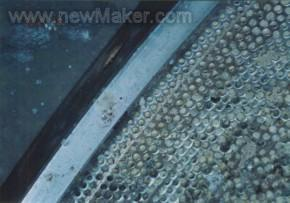
Due to the large size of the mold and the distribution of the die holes on the outer circle, the test point is a curved surface. The distance between the hole and the hole is generally 3 to 4 mm. Under these conditions, the Leeb hardness tester is used in a variety of applications and compactness. Convenient features can accurately test the actual hardness at the die hole. According to the measured hardness and the metallographic analysis of the test block, the process can be modified and developed more rationally, the material potential can be fully utilized, and the service life can be improved. For example, if a ring mold can produce 10 tons of feed in one hour, 100 tons of feed can be produced when the service life is extended by 10 hours, which will bring huge economic benefits to the company.
Third, the tool failure analysis of the Leeb hardness tester material 5CrMnMo large-scale hot forging die in the use of the cavity due to early wear, collapse and failure. As shown below:
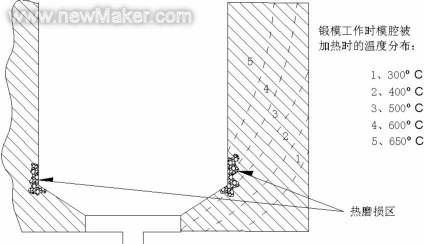
When testing the hardness of the wear zone with a Leeb hardness tester, the hardness value of the grinding was found to be lower than the hardness (38-42HRC) tested before use, in the range of 32-34HRC. This shows the second stage of the heating of the cavity in the red hot blank (>10000C) (the heating of the blank in the cavity can be roughly divided into four stages), when the heat is about 80% to 85%, due to the cavity wall Thick heat dissipation is slow, and the temperature of some spots is as high as 6500C or more. When the mold cavity is heated due to conduction, the temperature exceeds the mold tempering temperature, the mold is in the process of continuous tempering in the working process, and changes in the structure and properties will continue to occur, resulting in a decrease in the hardness value of the wear area and the occurrence of heat Abrasion indicates that 5CrMnMo, a hot work die steel, is not suitable for large molds. It is more suitable to use hot working die steels such as 3Cr2W8V, 3Cr3Mo3VNb, such as thermal stability, thermal strength, and yield strength when using 600~6500C hot working molds in the temperature zone than 5CrMnMo.
As China's industrialization process is still far from being completed, there is an urgent need to strive to shorten the gap with the international advanced manufacturing level. As an enterprise must recognize the heat treatment industry from a strategic perspective, not only from the equipment, processes, and especially testing equipment, the need for continuous Drawing on new technologies at home and abroad depends on actual production and application in heat treatment companies. This is a very sensible move, because there are five-year transitional periods for the WTO rules after China’s accession to the WTO. This is a critical period for China's manufacturing industry. The key reason is that it is because of China’s manufacturing after the transition period. Industrial companies will basically be in the same competitive position as foreign large companies, and during this transitional period, we can still fully prepare to enhance our competitiveness. Therefore, this is a very urgent requirement for companies.
Aluminum T Slot Profile
Aluminum T Slot Profile is a kind of aluminum extruded profile which has a special size.With the rapid development of China's large-scale infrastructure investment and industrialization process, the output and consumption of aluminum profiles in the whole industry has increased rapidly, and China has become the largest Aluminum Profile production base and consumption market in the world. After nearly 10 years of rapid growth, China's aluminum profile industry has entered a new stage of development, and has shown many new development trends.
Aluminium extruded Profile,Aluminium Slot Profile,T Slot Aluminum Profile,T Slot Aluminium Extrusion
Trumony Aluminum Limited , https://www.szaluminumpipe.com